An in-depth Q&A: Way more than three reasons to love 3D guitars from Customuse
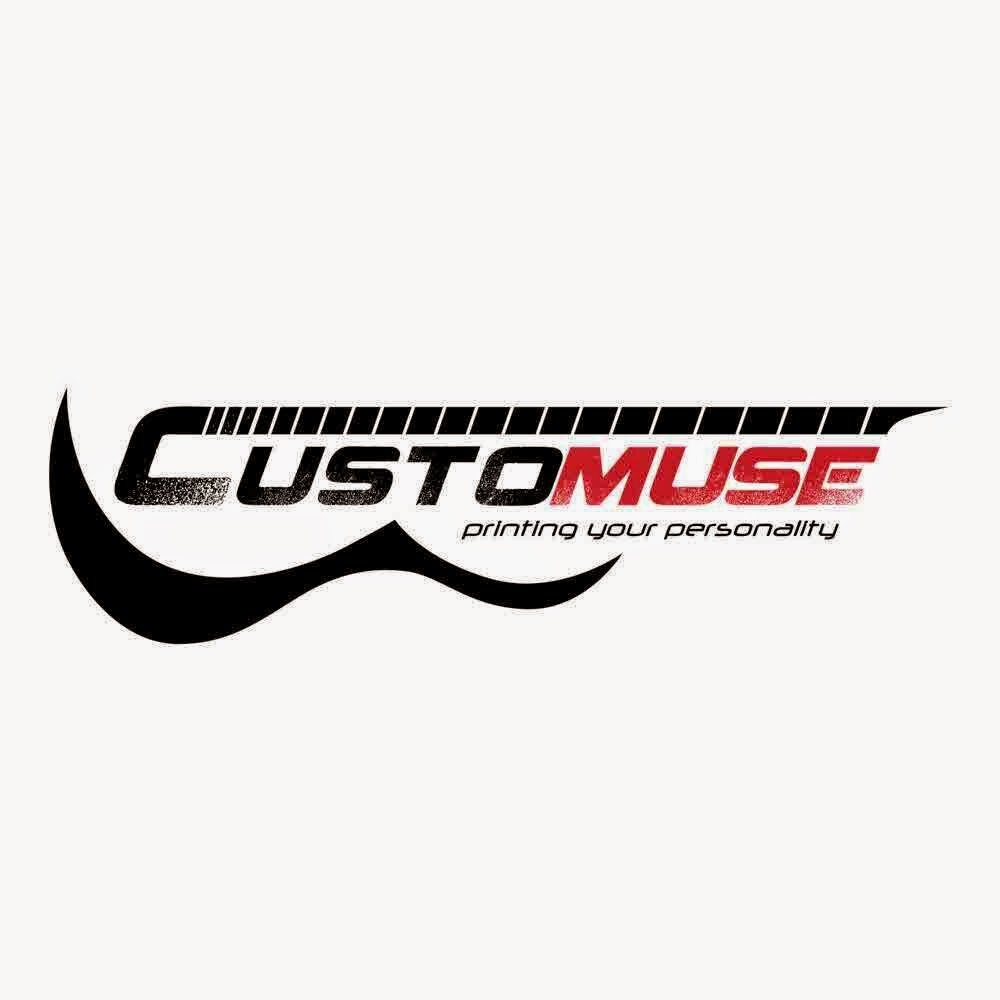
“If you imagine it [for a guitar], we can make it!”
Customuse Founder, Mahdi Hosseini
Art (and subsequently creativity) being a medium steeped in the very concept of uniqueness, it is not entirely surprising, between the rise of more personal 3D printing and the influx of start ups coming to successful fruition nowadays, that a company focused on the meticulous production of tailor-made, affordable guitars would eventually step onto the scene. Customuse, a London based, fledgling company looking to bring high level craftsmanship to more than A-list stars, has burst out of the gate with 3D printed guitars that have effortlessly grabbed the public’s attention; thanks to vibrant color, atypical design and of course, a strong instrument sound.
Founded by E-commerce, IT and software expert, Mahdi Hosseini, Customuse is all about the evolution of the guitar alongside 3D printing technology and this collaborative team of business professionals, musicians, scientists and sound engineers has taken one of the world’s most commonplace and popular instruments to a more complex plane — both in terms of aesthetics and its undeniably high ceiling of functionality. (Have you heard, the BBC reported this month, that electric guitar now overtakes the violin with the interest of music students!)
Hosseini, and Customuse’s resident guitarist, Ben Tannahill, who both recently shared the work of Customuse at Music Tech Fest in London, spoke with me and pulled back the curtain on what makes Customuse so appealing. We talked everything from the company’s approach to the product’s market value and the guitar’s performance capability, as well as what makes the team tick and where Customuse hopes to take its vision as the company grows and 3D printing technology gains a wider foothold in public use.
Mahdi Hosseini: The reason I believe our company will have a successful business, in terms of trying to compete with the other companies, and basically open up our position in the marketplace, is that what was available up to the point was, first of all, too expensive, and also, there was no customization. [Guitars] were 3D printed but they weren’t customizable. I kind of thought [other companies] were missing the point of 3D printing. You see, what really differentiates normal guitars from 3D printed guitars…is that traditional manufacturing is cheap to create a lot of guitars that are exact copycats of each other. But with 3D printing, it is not that cheap to print one guitar. If you print 10,000 of it, each of them is not going to be as cheap as the normal manufacturing. But if you print two different guitars, it is much cheaper than traditionally creating two different guitars. So actually, 3D printing is only very competitive on the basis on customization. We decided to get into this space and add the customizability – it’s kind of our mission statement.
Hosseini: At the moment our models are limited because we’ve just started out doing what we do but, the goal is that when we fully launch, there will be two different options. So if for example, you’d like the start with a template and be able to customize it to some level and basically just print it out, that would be our standard range, which is where most people probably fall in because most people like to have somewhere to start from, as opposed to absolutely starting from zero; especially if they’re not experienced guitar players or, they might not exactly know what they want. We’re trying to build this platform where, let’s say, you decide, “I want this [guitar] body,” and then you would pick what design you would want in it. So you could decide you want a certain overall shape but with a design from another shape.
We’ll have a selection of 10 different designs at least, trying to appeal to different subcultures. For example, our skull design kind of fits into the rock and roll [and] metal subculture, we have one that’s more abstract, we’re making one that’s called, “Steamuse.” It’s sort of steam punky; it’s has moving gears and everything and we’ve got a country [themed] one…so you can pick the overall design and then change the colors of different parts or you can add or remove small things to the model without knowing how to do anything in design.
[Conversely,] if you were a premium customer where you say, “No, I want a guitar that looks like a box of cereal and has my picture on it,” what we would do is if you’re in the UK you can come into our office in London or you could do a Skype interview where you would sit down with one of our award winning designers and then you would just tell them what you want and they would come up with sketches that are closest to [what you imagined]. But we have both, so depending on how much you want to customize, we can go all the way. …We’re currently working with this agency who created [the] platform for this website and the agency is going to build a very similar platform for us, so through that you can see what [we’re envisioning] with our customization platform.
Hosseini: Sound is a very subjective thing to start with. It’s not like I could rate it, scale it 1-10 and have it be universally true from everybody’s perspective…but the way we try to get the really top quality is that we have, on our advisory board, a mechanical engineer, who was the first mechanical engineer in the UK to design a 3D printed guitar. Also we have our sound engineer, Jason [Sanderson], he worked with Ginger Wildheart and Courtney Love…
…So the way we tested [the guitar] is that we took it to his studio, he’s got this church in Northern England that he turned into a studio…[at the time he] was recording a new record there and basically [the band] were using a normal guitar and they then also re-recorded the same chorus with one of our guitars [of the same model], the “Sunrise” [design], and they liked ours more, so they just mixed that [take] into the track. …So it’s all very subjective but in terms of musicians being happy with the quality, we have that and we [also] we try to compare it to other instruments, try to get the same sustain, the same resonance for the same notes and match it up.
We also [work with] Professor Neil Hopkinson…he’s affiliated with the University of Sheffield and he’s actually one of the inventors of the latest 3D printing technology, which is not even commercial yet. What [Hopkinson] has done, is created technology that [he explains,] “has the potential to make parts at a rate 10-100x faster than comparable laser technology today” and instead of burning the printing material with a little tiny laser, he’s created technology so it melts [material] one whole layer at a time…it’s a lot faster. Imagine you’re trying to fill in an area with a small pen and then filling in the same area with a very big pen. There’s a lot of work that goes into making sure they sound like a real guitar, not just look good.
Hosseini: When we did the very first guitars, we were really experimenting and when you do a 3D model there is a lot of simulations you could do in terms of [asking], “Is this going to be strong enough?”, “Are there any weaknesses or anything like that?” And there’s only so much you can do before you print it out and when we first printed it out, we didn’t know what the exact thickness was that we had to have…Basically what happened is that some parts of those guitars where slightly bendy if you pressured them hard enough because it was very think in parts. But then we changed our 3D model to be more robust and kind of compensate for that so that it doesn’t run into that issue unless you smash it into the ground.
Ben Tannahill: The sound is incredibly solid. The reason for this is, first, you have a central block of wood which is connected solidly to the neck. Really, really awesome sustain, and a really thick sound. Also, and I think Mahdi pointed this out, if you think about electric violins, the body isn’t that important. An acoustic guitar would be very, very different…you’d have to worry about the body a hell of a lot more. Whereas, with an electric guitar, there are loads of crazy guitars from the 80s, which have really weird bodies and no one accused them of [having bad sound.] Like, Michael Angelo Batio, he has this series called “Speed Kills,” where he’s got some ridiculous silver, rocket guitar, and Flying-V guitars, they have very little body on them but they’re still a favorite of rock stars. So you don’t need a really massive, solid body. Otherwise the best guitars would be the ones with the thickest, fattest bodies. And you don’t see Slash going around with a giant chunk of wood after all.
It’s sort of a lot about the quality of the neck and the quality of the construction and the pickups and the bridge and the strings and how well you play it. All this comes together to make the difference, rather than the fatter the body and “It’s not made of wood.”
Hosseini: [Another] thing that’s different about our guitars is that you know a normal, solid body guitar, say an SGR Fender, it’s never built out of a solid piece of wood. It’s always built out of two or three or multiple, depending on which range you buy. As a result of that…where the pins and all the components for your bridge go is not necessarily in the same piece of wood. It’s all stuck together with glue and everything but because our wooden block is just slightly thinner, it’s possible that we make it our of a single block of wood. So then it’s more consistent.
Tannahill: I’m a bit of a shredder myself so what I would personally go for is Humbucker EMGs, 8185’s, they’re like the active, active EMGs. They’ve got some serious distortion…[From the Sunburst guitar here], this is a really nice neck but I reckon if you have a wizard two neck like Ibanez have or something similar…just one of these really, really thin necks. Like the thinner [it is], the faster you can play. And like, a floating bridge so you’ve got a whammy bar. These are all things that could hopefully occur in the future. So if you’ve got a 7-string, a floating bridge, some EMGs, a really thin neck, with some really really whacky headstock, like, you’d have a seriously cool guitar, in my opinion.
Hosseini: [Aside from what we’ve discussed], we’re looking forward to doing a crowd funding campaign soon…about three months from now, just before Christmas. It would fund our operation to basically go full scale, which means we’d be able to build that customization platform, add more models to it and basically scale up our operations to where [something like Ben’s dream guitar] this would be a normal request because we would have many, many different combinations that somehow we could fit [that] into it.
Hosseini: Absolutely Slash!
Hosseini: The way it works right now, we don’t do direct payments so you have to get a quote from us and say you’re based in the US, we’ll just give you a quote for dollars. The other thing for people in the US is that you don’t pay VAT, which is cool. I mean, it depends on which state you’re in, you’re probably going to have to pay some sort of import tax but it’s [most likely] less than 20%. We do ship internationally so that’s not a problem.
Leave a Reply